Introduction: NdFeB magnets are used to produce blanks from ingredients, to further processed products, and finally to sales. Do you understand these processes?
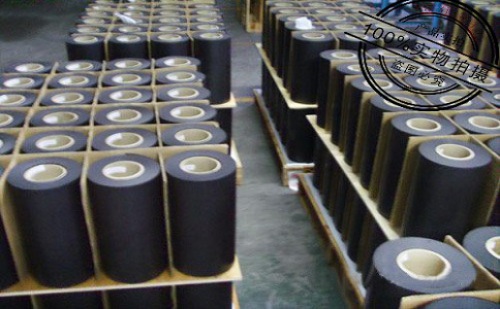
1, raw material preparation and pretreatment:
Process Description: Pretreatment of raw materials such as weighing, crushing, cutting and rust removal.
Process equipment: steel cutting machine, drum polishing machine, etc.
2, smelting:
Process Description: After pretreatment, raw materials such as yttrium, pure iron, ferroboron, etc. are proportioned and added to the vacuum melting furnace. After the high-temperature smelting under the protection of argon gas, the stripping is performed. The composition of the product is uniform, the degree of crystal orientation is high, the consistency of the structure is good, and the formation of barium-Fe is avoided.
Process Equipment: Vacuum Melting Furnace
3, hydrogen explosion:
Process Description: The hydrogen detonation (HD) process utilizes the hydrogen-absorbing characteristics of rare earth intermetallic compounds to place neodymium-iron-boron alloys in a hydrogen atmosphere. Hydrogen enters the alloy along a thin layer of cerium-rich phase, causing it to expand and burst and break along. The cracks in the cerium-rich layer ensure the integrity of the grain boundaries of the main phase and the yttrium-rich grains. The HD process makes the NdFeB sheet very loose, which greatly improves the milling efficiency of the jet mill and reduces the production cost.
Process Equipment: Vacuum Hydrogen Processing Furnace
4, milling:
Process Description: Air-milling powder is crushed by the high-speed collision of the material itself, and it has no wear and no pollution to the inner wall of the grinding mill. It can produce powders with high efficiency.
Process equipment: jet mill
5, molding orientation:
Process Description: The role of orientation is to change the c-axis of the easy-magnetization direction of the chaotically oriented powder particles to the same direction, thereby obtaining maximum remanence. The main purpose of press-type is to press the powder into a shape and size of crushed, while maintaining the degree of orientation of the grains obtained in the orientation of the magnetic field as much as possible. We designed the secondary molding using a magnetic field molding machine and an isostatic press. For special-shaped magnets, special tooling equipment is used for direct molding. The sintered magnets can be put into use only with a slight surface treatment, which greatly saves materials. And subsequent processing costs. Process Equipment: Magnetic Field Press, Isostatic Press
6, sintering:
Process Description: Sintering is a series of physical and chemical changes caused by crushed under high temperature, is a simple and inexpensive method that can change the microstructure of the material to improve the magnetic properties of the material. Sintering is the final shaping of the material and has a very important influence on the density and microstructure of the magnet.
Process Equipment: Vacuum sintering furnace
7, machining:
Process Description: The NdFeB magnets obtained after sintering are all blanks and require further machining to obtain products of various sizes, sizes, and shapes. NdFeB magnets are relatively brittle and have poor mechanical properties. Generally, they can only be ground and machined.
Process Equipment: Surface Grinding Machine, Double Face Grinding Machine, Chamfering Machine
8, surface treatment:
Process description: Surface treatment of rare earth permanent magnets of various shapes, such as electrophoresis, galvanizing, nickel, nickel-copper-nickel, and phosphating, to ensure the appearance and corrosion resistance of the product.
9, finished product inspection and packaging:
Process Description: The product's various magnetic properties, corrosion resistance, high temperature properties, etc. are tested and packaged after reaching the standard to meet the various needs of customers.
We provide organic and inorganic pigments to our customers in Middle East, South East Asia etc,you also can find barium sulphate, carboxyl methyl cellulose , melamine and other relative producets here.
Iron oxide red is widely used as inexpensive, durable pigments in paints, coatings and colored concretes.
1. barium sulphate, it is super-fine powder made from high quality barite which is after thoroughly grinding process. The end products have good dispersibility, high whiteness, nice covering power, stable chemical properties.
Application : used in pharmaceutical industry, leather industry, printing and dyeing industry
2. Melamine:
Main Application, Storage and Transportation:
1). Food grade melamine raw material can be used to produce melamine table ware.
2). Also used as industrial grade additive, widely used in plastics, paint textile, paper.
3). Used as the material to produce melamine formaldehyde (MF) colophony.
4). Owning the abilities of fire-resistant, water-resistant, hot-resistant, age-preventing, electric arc resistant, bearing chemical corruption, perfect insulation capability, gloss grade, and machinery intention, and good thermal-setting capacity, it is widely used in wood, plastic, dope, paper-making, textile industry, leather, electric, and medicine, etc.
5) The product is a kind of weak alkaline and nontoxic material. It should be kept in a clean and dry place. Moisture and rain proof with careful handle during storage and transportation.
White Powder Pigment,Waterproof Coating,Pigment Ink,Iron Oxide Pigments
Gemhold (SJZ) Trading Co., Ltd. , https://www.gemhold.cn