Abstract: Combining the technical application methods and typical process characteristics of domestic major automotive panel manufacturers, from digital measurement technology, CNC machining tools, CAM software, mold heat treatment technology and CAD/CAPP/CAM/CAE seamless integration of digital virtual manufacturing. The intelligent manufacturing of automobile cover moulds was discussed.
The automobile cover mold manufacturing technology has gradually matured in China, and has gradually shifted from the extensive development model mainly relying on scale expansion and quantity increase to the lean development model mainly relying on scientific and technological progress and improving product quality and level; The development model based on the introduction and digestion of international advanced technologies will be transformed into a development model that combines digestion and absorption and enhances independent innovation capabilities; from industry-based industry characteristics to technical and modern enterprise management. Characteristic transformation; we are vigorously promoting innovation-driven development methods and actively cultivating and developing new growth points. Mold companies have changed from pure production to production services. Due to the continuous increase of labor costs in industrialized countries, it is forced to transfer molds to developing countries, especially countries with better technical bases like China, in order to reduce production costs. Foreign companies have bred their base chemical plants in China. In the international market, the trend and market share of multinational companies to purchase molds in China continues to increase, and the development of technology in the mold industry has entered an era of accelerated competition. All mold companies have increased their investment in advanced technologies. Combined with the 2016 Shanghai International Mould Exhibition, it introduces several main features of recent advanced technology in the application of automotive panel moulds.
1. Digital measurement technology is widely used
In the past, the detection of the cover molds mainly focused on the inspection of the profile and the inspection of the inspection tools. The detection of the process control and the structural parts were limited by the influence of the detection equipment and the detection method, and were not widely used. In recent years, with the improvement of detection technology, digital measurement has shown a trend of rapid popularization. Measuring instruments are moving towards field, digital, automation and intelligence.
(1) Diversification of measuring instruments: Blu-ray automatic scanning of the latest technology in the field of field, automation and digitization, automated photo-based white light measurement system using robot to improve measurement efficiency, 360° intelligent online measurement integrated with camera measurement system and robot The solution to achieve automated inspection and quality control is the focus of mold inspection (see Figure 1).

(2) The traditional detection tool realizes digital measurement: digital measurement wireless transmission of measuring instrument, measuring instrument → computer data processing → detection report (see Figure 2).
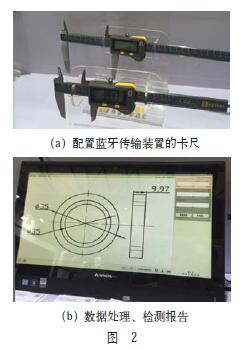
(3) Mold normal structural surface inspection gage: 1 manual measurement gage measuring instrument (caliper, micrometer and dial gauge, etc.). The accuracy of the mold surface inspection requirements is met, but it is difficult to meet the measurement requirements of the normal structure three-dimensional data from the functions (the caliper and the micrometer have the range limitation), and the manual measurement efficiency is low. 2 Optical measuring equipment (shooting, scanning). From the function, it can meet the three-dimensional measurement requirements of the normal structure, and can complete the inspection on the shop floor, but the detection accuracy can not meet the structural surface accuracy requirements. 3 large-size three-dimensional precision measuring equipment - three coordinate measuring machine. The portable articulated arm measuring machine (see Figure 3a) can solve the three-dimensional measurement requirements of the normal structural surface of the shop floor, but the measurement accuracy can not fully meet the dimensional accuracy requirements of the normal structure of the mold; the gantry type CMM (see Figure 3b) can meet Various testing requirements for the mold, but it requires a constant temperature measuring chamber. The use of the gantry three-coordinate measuring machine has high cost, strict maintenance requirements and economical generality. From the perspective of measurement accuracy, the detection requirements of large molds can only be met by a CMM. In the future, the measurement method and measurement accuracy will be improved to make the measurement work more perfect.
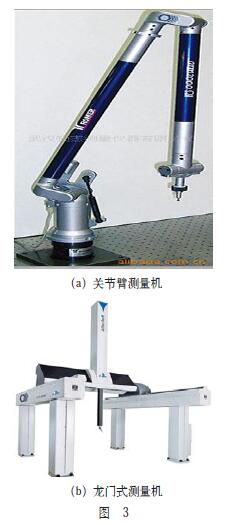
2. CNC machining tools are diversified, high precision and high performance
The new high-quality slender hot-fit tool holder with two-dimensional curve is a highlight of the exhibition (see Figure 4). The rigidity of the tool holder is 3 times that of the integrated tool holder, and the end of the tool holder is thick. It can be as small as 1.5mm and can reliably meet the requirements of high-precision 5-axis machining. High-precision and powerful chucks and carbide rods are the main theme of most exhibitors. This is also the mainstream of mold processing tools. The tool coating technology is widely used, and the corresponding model products are produced according to the characteristics of the parts, making the numerical control processing quality control easier to realize.
3. CAM software integration, networking and intelligence
With the popularization and application of CNC machine tools, the factory has a certain number of CNC machine tools, including multi-axis precision CNC milling machines. The core products of the factory are basically manufactured by full digital chain CNC machining, mainly on precision machining centers, even in integration. The flexible manufacturing unit is completed and the plant will introduce more multi-axis processing equipment and flexible manufacturing units in the future. However, the factory is relatively backward in numerical control programming software and processing strategy. With the increasingly fierce competition in the mold market, the casting cycle and quality of the mold have higher requirements. The automation, refinement and standardization of CNC machining have become the mold industry. The development trend of manufacturing technology. Fine surface design technology, high-precision CNC machining technology, and A-level surface modeling technology are all problems that need to be solved at the current or next stage. Powermill, Tebis, worknc, CAXA, Zhongwang and other domestic software developed the latest version of the software in 2016. The VERICUT and NCBrain processing simulation software functions also have corresponding function updates. The characteristics of software technology to integration, networking and intelligence are becoming more and more obvious (see Figure 5). The Tebis booth has a large scale. The new version of Tebis has corresponding solutions for the bottleneck of 2D programming of molds in production and the 2D automation programming and automatic processing of molds.
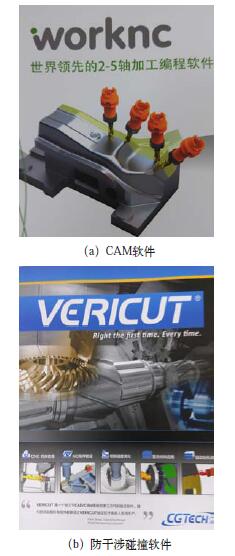
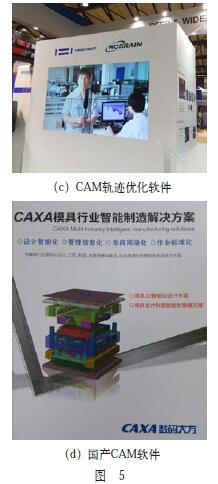
4. Mold production is gradually developing towards intelligence
Lean manufacturing equipment and automated intelligent manufacturing and integrated molding and precision mold manufacturing. On the basis of the original high-end precision processing equipment and technology, new technology applications such as 3D additive manufacturing, laser equipment and robot automation integration will be injected, and will be extended to new formats such as Internet mold, mold making and cloud manufacturing ecosystem. The new features of “fine, automated, information, integrated, networked, and intelligent†(see Figure 6).
Molds have evolved from basic process equipment to information-based, intelligent integrated manufacturing units, from single-function process equipment to providing integrated solutions for customers. Providing SE services to OEMs and body-in-white solutions based on modular, inspection and clamping has become one of the core competitiveness of mold companies.
5. Development of mold heat treatment technology
At home and abroad, the mold manufacturing industry is developing in the direction of informationization, non-image, refinement and automation. Advanced technologies such as CAD and CAM have been widely used in mold manufacturing. As an important part in the mold manufacturing, the quality of the mold material and the deformation after heat treatment have seriously restricted the precision and efficient development of the mold industry.
With the adjustment of the product structure of the mold, the cast product has an increasing proportion in the mold due to its low material cost, low processing volume and convenient processing technology. At present, the selection of cast iron materials for large and medium-sized stamping dies abroad is a trend in the future.
As a commonly used heat treatment method for foundry products, surface flame quenching has been widely used due to its low cost and convenient operation. However, with the development of high-tech, the defects of traditional manual flame quenching quality and deformation are gradually highlighted, and the precision machining, grinding and welding measures taken after quenching not only increase the processing cost, The tool is consumed and the machining cycle is delayed. The use of laser quenching technology (see Figure 7) can effectively solve these problems.
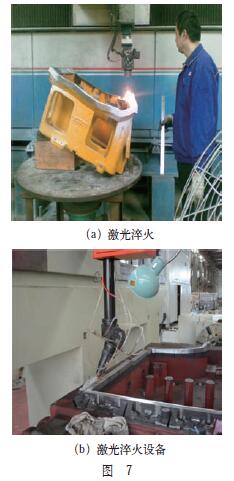
Laser quenching is a high-tech that uses a focused laser beam to rapidly heat the surface of a metal material to cause a phase transformation to form a martensitic hardened layer. Laser quenching is a rapid heat treatment, self-excited cooling, without tempering, is a pollution-free and environmentally friendly heat treatment process. The heating speed is fast, the heat affected zone is small, the deformed mold is small, and it is suitable for high-precision parts processing, and some occasions can be used as the final processing procedure of materials and parts. Laser quenching can adjust the depth of the hardened layer as needed. The depth of the hardened layer is generally 0.3 to 1.5 mm, and the quenching is uniform, and cracking is not easy. Laser-quenched martensite grains are finer, have higher dislocation density, higher hardness and better wear resistance.
The mold part shown in Fig. 8 adopts the surface flame quenching deformation amount>1.5mm, and the laser quenching deformation amount is <0.05mm.
The surface flame quenching process is: profile roughing → profile contour semi-finishing → the fitter needs to be quenched from the bottom plate → flame hardened → fitter training bottom surface, joint surface and top surface → assembly to bottom plate → profile profile Finishing → commissioning. The laser quenching process is: profile roughing → profile contour semi-finishing → profile contour finishing → laser quenching → commissioning.
Process comparison: Laser quenching can reduce three process flows, and the profile profile is finished without quenching. After laser quenching on a large outer cover mold, the amount of deformation of the fitter is greatly reduced due to the extremely small deformation of the profile after quenching, and the mold manufacturing cycle is shortened.
6. CAD/CAPP/CAM/CAE seamless integration of digital virtual manufacturing
The CAD/CAPP/CAM/CAE process is centered on product processing data. The same data flow is used for CAE simulation analysis, mold design, mold NC machining, and mold CMM (three-coordinate) inspection. The process documentation for the workshop can be directly generated by CAD. Transfer to CAPP to maintain a high level of consistency between the final mold product and the designer's intent. This is the CAD/CAPP/CAM/CAE integration technology. The identity of the three-dimensional model guarantees the closed-loop characteristics of the CAX chain, making it difficult to generate design and processing errors, thereby improving the development efficiency of the mold. The seamless integration of CAX makes virtual manufacturing technology a reality, fundamentally changing the traditional manufacturing model of design, trial production, modification design, and scale production. Before the product is actually produced, it first predicts and evaluates its performance and manufacturability in a virtual manufacturing environment, thereby shortening the design and manufacturing cycle of the product, reducing the development cost of the product, and improving the ability of the system to respond quickly to market changes.
7. Conclusion
With the continuous improvement of the technical level, domestic mold manufacturing enterprises have narrowed the gap with the international advanced mold manufacturing regions. The advantages of mold companies from price competition are gradually weakened. In the future, they must break through in terms of technology and management. Each mold company still needs to constantly explore.
Fatty Alcohol Polyoxyethylene Ether Sodium Sulfate
Raw Materials Of Detergent,Surfactant Raw Materials,Application Of Foaming Agent,Fatty Alcohol Polyoxyethylene Ether
XINGZHILIAN BIOLOGICALR&D CO.,LTD , https://www.xzlsdslds.com